- Release of toxic/flammable materials
- Explosion
- Fire

Union Carbide India Ltd (UCIL), Bhopal, India, 02 December 1984
SUMMARY
At 11.00 pm on 2nd December 1984, an operator at the plant noticed a small leak of highly toxic methyl isocyanate (MIC) gas and increasing pressure inside a storage tank. The vent-gas scrubber, a safety device designed to neutralize toxic discharge from the MIC system, had been turned off three weeks prior. Apparently a faulty valve had allowed one ton of water for cleaning internal pipes to mix with forty tons of MIC.
A 30 ton refrigeration unit that normally served as a safety component to cool the MIC storage tank had been drained of its coolant for use in another part of the plant. Pressure and heat from the vigorous exothermic reaction in the tank continued to build. The gas flare safety system was out of action.
At around 1.00 am, December 3, loud rumbling reverberated around the plant as a safety valve gave way sending a plume of MIC gas into the early morning air.
The effect was devastating as within a short period people and animals started dying. The cloud of toxic gas drifted towards the south and it is reported that within 4 minutes that the cloud reached an area some 2 km from the plant, 150 people died, 200 were paralysed, 600 rendered unconscious and some 5000 were severely affected.
LESSONS
- Plant Siting
- Site was close enough to populated areas prior to building of plant.
- Housing developments had been built around the plant over the years and although these were illegal in the first instance, they were acquiesced by the Indian authorities.
- Management of major hazard installations should be carried out by a suitable competent management.
- Need for appreciation of the hazard from the high toxicity of a substance.
- Need to pay more attention to runaway reaction in a storage tank. Where this reaction could act as a dispersion mechanism of a hazardous substance, it should be carefully reviewed.
- The hazard of water in plants is generally well known, but attention needs to be given to it when it can lead to explosive forces due to vaporisation or exothermic reaction with a process fluid.
- The hazard of materials in storage should be properly assessed. Although materials in process are generally considered riskier, inventories of stored materials are usually larger.
- Priority between safety and production
- Measures to cut costs had been taken prior to the accident in the plant. Some of these could have influenced the development or consequences of the accident.
- Limitation of inventory in the plant: smaller amounts of toxic substances should be considered when large inventories are not necessary.
- The problem of setting a high set pressure of relief devices need to be appreciated when cause of potential pressure rise is a runaway reaction.
- The effect of the disabling of safety critical systems need to be recognised. It is essential that there are strict procedures for disabling any item which is critical for protection of the plant. The flare system was out of commission for 3 months prior to the accident.
- Good maintenance of plant equipment and instrumentation is required as part of a fire and explosion hazard management strategy.
- Leaking valves and malfunctioning equipment was common throughout the Bhopal plant.
- Proper isolation procedures for maintenance were not followed at the plant.
- The effect of control of plant and process modifications need to very carefully looked at.
- Authorities, emergency services, workers or members of the public exposed to dangerous substances should be fully informed of the hazards.
- An emergency plan needs to be in place for major accident scenarios. There was no effective emergency plan in place at the Bhopal plant.
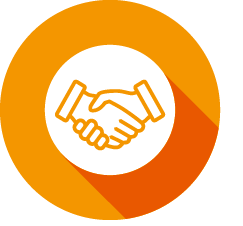