- Release of toxic/flammable materials
- Explosion
- Fire

Grangemouth Refinery, Grangemouth, UK, 29 May 2000
SUMMARY
29th May 2000: All power was lost to 3 electrical substations that supply electrical power to the North Side of the Complex which contains the Oil Refinery, various chemical plants, utility plants and logistics facilities. Emergency shutdown of the Oil Refinery and the chemical plants on the North Side occurred and the utility plants were also affected due to a loss of power to the main cooling water pump systems. In addition because of the duration of the power failure, a controlled shutdown of some other facilities elsewhere on-site was also necessary because the supply of steam for the correct operation of the flare system could not be maintained. No injuries resulted.
7th June 2000: An 18 inch medium pressure (MP) steam main located near to a road ruptured resulting in a significant loss of MP steam directly into the atmosphere. The steam leak damaged fencing immediately adjacent to the ruptured pipework. Debris and steam was blown across the road until the leak was isolated. The leak also caused significant noise being heard in the Grangemouth area. There was significant disruption to the steam supply system for the Complex for approximately one hour until the steam leak could be isolated.
10th June 2000: The Fluidised Catalytic Cracker Unit situated on the Oil Refinery had been shut down on the 29th of May following the power distribution failure. During start up procedures on the 10th of June, there was a significant leak of hydrocarbons from the Fluidised Catalytic Cracker Unit (FCCU or Cat Cracker) creating a vapour cloud which ignited, resulting in a serious fire. On and off-site emergency services were mobilised and the fire was brought under control in approximately 90 minutes.
During the fire and in the fire-fighting efforts, some damage resulted to asbestos cladding surrounding pipework and vessels. Some hydrocarbons in the contaminated firewater run-off were discharged directly into the River Forth.
No injuries occurred to the workers in the vicinity. However, there was the potential for injury to people and greater damage to equipment.
LESSONS
- Major accident hazards should be actively managed to allow control and reduction of risks. Control of major accident hazards requires a specific focus on process safety management over and above conventional safety management.
- Specific consideration should be given to adopting robust “management of change” procedures with all changes – including organisational changes – being fully evaluated before implementation to ensure that all potential hazards associated with the change have been identified.
- Avoiding a loss of containment is important not only for pressure vessels and other large items of plant and equipment but also for the pipework systems which are often not subjected to the same rigorous levels of inspection and maintenance. A reduction in the number of flanges, the removal of dead-legs, a reduction in vibration and the correct securing and supporting of pipework systems can reduce the likelihood of a loss of containment and hence the probability of a major accident occurring.
- Companies should develop key performance indicators (KPI's) for major hazards and ensure process safety performance is monitored and reported against these parameters.
- Conventional indicators of safety performance such as “days away from work” (which are high frequency/low consequence events) do not give a measure of process safety relevant to the control of major accidents (which are low frequency/high consequence events) and may give a false impression of process safety performance.
- Companies should benchmark their performance in relation to the control of major accident hazards against industry standards
- Disruption to utility supply systems (steam, electricity etc.) on a major hazard site can cause significant problems and have the potential to result in a major accident
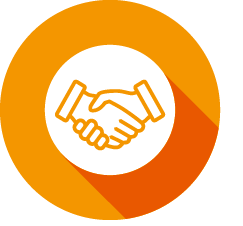