- Release of toxic/flammable materials
- Explosion
- Fire


Phillips 66 Company, Pasadena, USA, 23 October 1989
SUMMARY
Following the release of a gas mixture, a vapour cloud formed and moved quickly downwind where it found an ignition source and exploded. There were several subsequent massive explosions involving two isobutane storage tanks and the catastrophic failure of a polyethylene plant reactor.
LESSONS
- Management of major hazard requires a good understanding of the hazards via hazard identification and assessment. No hazard analysis had been carried out for the installation.
- Plant layout and separation distances are essential elements of good plant design. Separation distances between process equipment were inadequate in the Phillips plant and hindered the safe escape of personnel. In addition, the control room was destroyed in the initial explosion as it was too close to the plant.
- Consideration should be given to the arrangement of ventilation intakes of buildings to prevent intake of gas in the event of a release.
- Minimising occupancy of buildings is an important factor in limiting exposure of personnel. Both the control room and the buildings at the Phillips plant had high levels of occupancy.
- Good fire and explosion hazard management strategy relies on multiple barriers including proper ignition control, detection systems, enforcement of safety procedures.
- Control of ignition sources at the plant was poor.
- There was no fixed flammable gas detection system despite the large flammable inventory.
- There was no enforcement of the Permit to work systems
- Violation of the isolation procedures for maintenance was a local practice that was not picked up by the safety audits.
- Mitigation measures must be properly designed to prevent failure during the event.
- The fire water system relied on the process water system and was vulnerable to an explosion.
- The electricity cables for the fire pumps were not laid underground and this increased their vulnerability to damage by fire and explosion.
- Emergency planning is an essential part of management of major accident hazards.
The company had a good emergency response plan. A series of joint exercises were conducted with the emergency services and this resulted in a good response on the day of the event. This was one of the most positive lessons learnt from the accident.
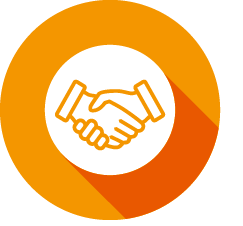