HSE HSL/2006/79
CFD Modelling of Water Spray Barriers
FABIG Members: Log-in to access all FABIG resources LOG IN
SUMMARY
The primary objective of this project is to develop a capability within HSE for modelling water spray barriers typically used in tunnels under construction using Computational Fluid Dynamics (CFD). This has involved a literature survey of existing experimental and modelling efforts and some trial CFD calculations. Details of the computational techniques involved in the trial CFD calculations have been included in the report to help inform future modelling efforts. The CFD model developed here is intended to provide qualitatively correct predictions but is not rigorously validated.
There is a significant body of literature on modelling fire suppression sprinklers and spray barriers used for dense gas dispersion, but relatively little aimed specifically at using spray barriers to control smoke movement. Computational models of sprays generally fall into two categories: Eulerian models and Lagrangian (or particle-tracking) models. The former type is generally faster to solve computationally but also assumes that water droplets behave as a fluid continuum. The Lagrangian approach involves tracking the progress of clusters of water droplets through the flow and is potentially more accurate than the Eulerian approach but can also be more expensive in terms of computing time. Examples of the application of both of these models are discussed in the report.
Trial CFD calculations have examined a range of spray configurations starting with a single, vertically-discharging spray. Reasonable agreement was obtained between the Eulerian CFD model predictions and experimental measurements although the predicted spray was closer in character to a hollow-cone than the solid-cone spray that it was supposed to represent. The Lagrangian model gave slightly better agreement with the experimental results. A number of progressively more complex configurations were then examined: horizontally-discharging sprays, two sprays impinging together and a simplified 11-nozzle spray barrier. Finally, simulations have been performed of a full spray-barrier configuration consisting of 18 nozzles to compare to the ongoing experiments at HSL. The Lagrangian CFD model was found to predict air velocities in the tunnel in good agreement with experimental measurements. Computing times for these calculations were relatively modest – an hour or two at most. It therefore seems feasible that more complex scenarios could be reasonably modelled.
Future work to further develop a spray barrier modelling capability should combine the spray barrier model developed here with a full-length tunnel model. This would include simulated blockages due to a tunnel-boring machine and a simulated fire producing a hot plume and smoke. A number of key issues would need to be addressed, such as evaporation of the droplets in the hot layer and cooling of the smoke. However, the papers reviewed for the literature survey in this report give some advice on how these features could be modelled. Such CFD calculations could provide a series of animations showing how smoke moves down tunnels in the event of a fire, illustrating how spray barriers disrupt the smoke layer. This could be used in conjunction with video footage from experiments to provide useful training material for personnel involved in the tunnelling and mining industry.
This report and the work it describes were funded by the Health and Safety Executive (HSE). Its contents, including any opinions and/or conclusions expressed, are those of the author(s) alone and do not necessarily reflect HSE policy
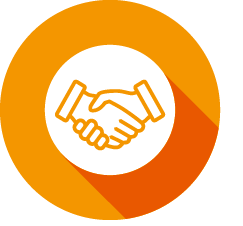