- Release of toxic/flammable materials
- Explosion
- Fire


Amuay Refinery, Falcón, Venezuela, 01 September 2012
DESCRIPTION OF FACILITY
The Amuay Refinery forms part of the Paraguaná Refinery Complex located in the Paraguaná Peninsula, Venezuela. Operated by the state owned Petróleos de Venezuela (PDVSA), it is the second largest refinery complex in the world, refining 955 thousand barrels per day and accounting for 71% of the refining capacity of Venezuela.
The Amuay Refinery itself is located in a residential and commercial neighbourhood. It was established in 1950 with a capacity of 60,000 barrels per day increasing over time to approximately 645,000 barrels per day with currently five distilleries . At the time of the incident and in addition to workers at the plant, several members of the National Guard were stationed for providing security to the plant. In the months leading up to the incident, the plant was shut down multiple times for minor incidents such as small fires and equipment failures.
ACCIDENT DESCRIPTION
During the early hours of 25th August 2012, a vapour cloud was detected during a routine inspection of the site and subsequently reported as an olefin leak from a storage area on site. The vapour cloud drifted South-East over a wide area for approximately an hour before finding an ignition source and leading to an explosion at 1:15am. The ignition source is thought to be the engine of a car that was started during evacuation. A series of large fires ensued, spreading to a total of three storage tanks which burnt until mid-day on 28th August.
The explosion resulted in the deaths of 48 people, most of these being National Guard soldiers stationed at the site. A further 151 people suffered injuries. Due to the refinery’s close proximity to residential buildings, the blast also damaged over 1600 homes, forcing residents to leave even once the fires had been extinguished.
Reports into the incident revealed that the leak was caused by the failure of a seal between the head and suction box of a pump located at the base of the “TK 208 and 209 areas”, although the potential causes of failure differ between reports into the incident, with both sabotage and poor maintenance blamed. Action was taken by workers to try to stem the leak by closing valves and shutting down equipment, but these actions proved unsuccessful given the size of the leak as well as that of the already formed vapour cloud.
Some workers and groups have claimed that despite the leak being reported an hour prior to the explosion, adequate emergency plans were either not put into place or were simply inadequate. This includes a failure to properly evacuate and the mishandling of contingency plans put in place for such an incident.
Despite the explosion, operations began to gradually resume at the plant from 30th August, with two production units producing 160,000 barrels per day. A third unit was restarted shortly after and full operational capacity was restored by the end of the year.
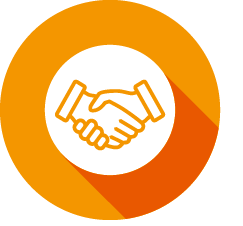